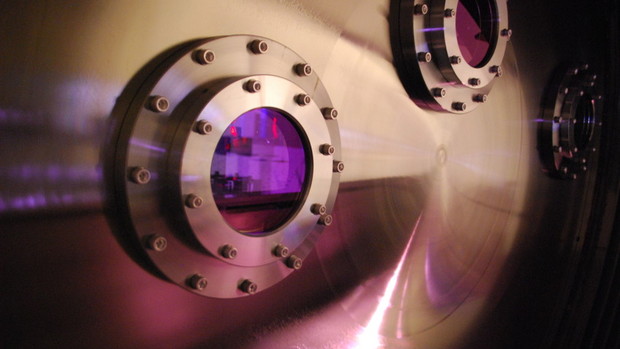
One of the view-ports through which LIGO engineers can peer into one of the "HAM" vacuum chambers, which contain LIGO's critical detector components. (Credit: Caltech/MIT/LIGO Lab/Kiwamu Izumi)
Ultra-High Vacuum
U.S. National Science Foundation Laser Interferometer Gravitational-wave Observatory (NSF LIGO) optical components quietly reside in a colossal vacuum chamber encompassing 10,000 cubic meters (353,000 cubic feet), with an air pressure of 10-9 Torr, or one-trillionth of an atmosphere. NSF LIGO's vacuum system is one of the largest and cleanest in the world, surpassed only by the vacuum system maintained by the Large Hadron Collider in Switzerland.
Creating and maintaining such a pristine vacuum is absolutely essential to LIGO’s operation. For the interferometer to detect the astoundingly small signals of passing gravitational waves, LIGO's laser must travel through the instrument unimpeded by anything (even on a molecular scale) that could scatter, refract, reflect, or absorb its photons. The extreme vacuum environment achieves this paramount goal first and foremost, but it is also essential for other reasons. It prevents sound waves from causing vibrations on the suspended mirrors (sound cannot travel through a vacuum). It also prevents temperature variations from occurring inside the tubes--variations that would change the shape LIGO’s optics enough to alter the path or destroy the quality of the laser beam. More fundamentally, removing any molecules and "dust" from the system ensures that no contaminants will land on any of LIGO's mirrors or other optics, which when struck by the laser, would be vaporized and cause irreparable damage. Considering that each test-mass mirror costs about $2 Million to manufacture, such an event would be a costly 'accident', and take the instrument out of commission until a replacement could be installed.
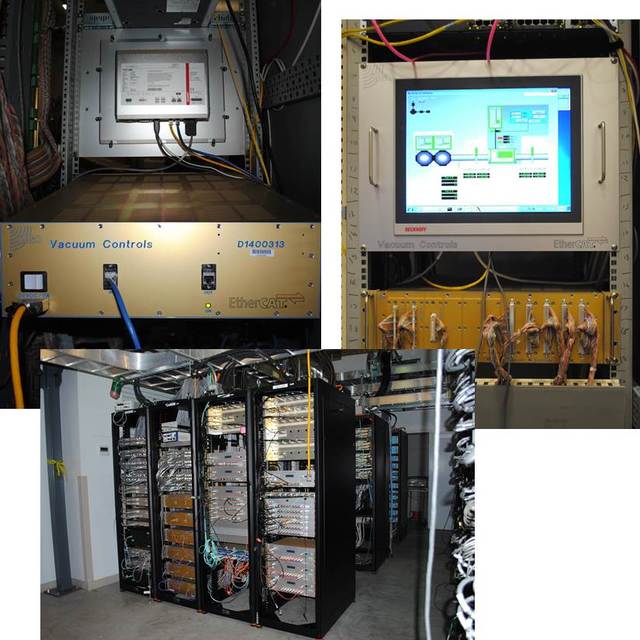
LIGO's vacuum system is controlled and monitored by multiple levels of sophisticated computing systems. The lower image shows the numerous racks of measurement equipment that monitor the buildings that house the vacuum systems, cryopumps, and ion pumps (among other things).
It took 1100 hours (40 days) of constant pump-down to evacuate LIGO's vacuum tubes to their ideal operating pressure. In that time, turbo-pump (jet) vacuums removed the bulk of the air in the tubes, while the tubes themselves were heated to 150-170 degrees Celsius for 30 days to drive out residual gases and moisture from the steel itself.
Maintaining the Vacuum System
Achieving the vacuum is one feat. Maintaining it at this level requires sophisticated monitors and controls, as well as continuous operation of ion pumps that extract molecules outgassing from the tubes and other structures and components that live inside the vacuum systems. Stray water molecules are also removed by continuously operating liquid nitrogen cryopumps; the water molecules stick to them.
Beam Tube Installation
LIGO’s vacuum tubes were constructed of spiral-welded 304L stainless steel. With its relatively low carbon content, 304L steel is resistant to corrosion, especially at the welded seams. It takes time to make tubes as large as LIGO's, and in the process of their manufacture in the 1990's, rust actually grew on their interiors. This meant that when the tubes were installed at LIGO, their insides needed to be meticulously polished and cleaned to remove the rust and significantly reduce the chances that steel-oxide flakes would end up in the vacuum system and fall into the path of the laser beam or land on mirrors or other optical surfaces.
LIGO's arms are long enough that the curvature of the Earth itself was a complicating factor when installing the vacuum tubes. It wasn’t enough for LIGO’s civil engineers to smooth a level path and assemble each arm’s tubes in a straight line. To ensure a perfectly level beam path, the Earth’s curvature (more than a vertical meter over the 4km length of each arm) was countered by GPS-assisted earth-moving and high-precision concrete work. Reinforced concrete floors, 75cm thick under the interferometers minimize leak-through of seismic vibrations. These floors are separated from slabs that support labs and offices, and from footings that hold the vertical framing. Each of these levels of engineering helps to isolate LIGO’s detector components (laser beam, optics, etc.) from terrestrial vibrations, which hinder the interferometer's sensitivity.
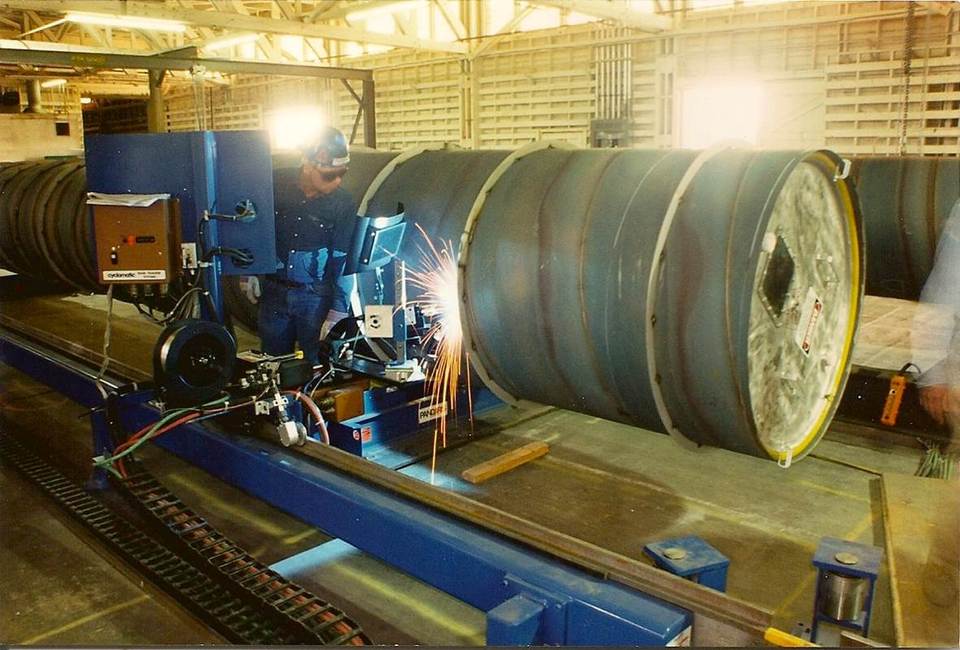
A segment of LIGO’s beam tube being assembled. Support rings are welded to the spiral-welded tube to greatly increase the structural integrity of the 3 mm thick steel. (Credit: Caltech/MIT/LIGO Lab)

Exposed beam tube after assembly at LIGO Livingston. The stiffener rings help to prevent the tubes from collapsing under the weight of the Earth's atmosphere. About 150-million kilograms of air are constantly pressing on the surface of the 4 km-length of each beam tube. (Credit: Caltech/MIT/LIGO Lab)
The 1.2m-diameter beam tubes were created in 20m segments, each one made from a continuous ribbon of 3mm-thick steel, spiral-welded into a cylinder resembling a paper towel tube. Stiffener rings were added to provide significant structural support to the tubes to prevent them from being crushed by the Earth's atmosphere, which exerts about 10,300 kilograms of pressure per square meter of tube surface. A testament to their manufacturer, the tubes have withstood these extreme stresses for over 20 years.